Solving Problems Saving Money
Dynamic Valve Services are valve and actuator experts.
We prefer face-to-face communication. While we often engage with our clients on the phone or by email, we always ensure that we meet them in person so they know us and we know them. Meeting in-person helps us to create a sense of security, establish trust, demonstrate our values, and build a relationship.
Off the hop, we gather information on whatever problem you’re facing by asking questions: What brand of valve or actuator are we dealing with? What is happening? How did it fail? Is it operating partially or not at all? By understanding the circumstances surrounding the failure as well as the equipment’s criticalness, we can assemble what we need and get to site right away. We always ask about products and brands so that we can source spare parts from our shop or manufacturers – plus it’s always best to be prepared.
When we arrive onsite, we discuss what happened, do up our permit and our field-level risk assessment, then pull out our tools or trucks onsite to troubleshoot and tend to the issue. Most of the time, we can fix the problem immediately, but occasionally, we provide temporary solutions that allow production to continue while we develop and implement a permanent solution.
Ultimately, we offer superior valve and actuator expertise. Our teams are meticulously and exhaustively trained on both common and uncommon problems so that they troubleshoot any and every problem. After every job – repair or replacement – we provide our clients with a comprehensive report on what we found, what we did, and how to proceed as far as warranty and preventative maintenance. We want to give our clients the tools to minimize downtime and manage budgets. Plus, we always follow up to make sure that everything is operating smoothly.
Get a Quote For Your Project
Valve Service and Repair
For actuators and well head (API) and pipeline (ANSI) valves, we provide both shop and field service and repair. In our shop facility, we have ten-ton crane capabilities, seven fully equipped service units, four hydrostatic test stands, and one remote hydrostatic test unit with capabilities from half inch all the way up to 60 inch in API and ANSI. All repairs, new, or reconditioned parts are tested before being sent out. In the field, our trucks are equipped to offer in-line valve and actuator repairs (and if our trucks aren’t stocked with the right parts, we’ll source them bring them out).
We also offer our clients a swap-out program where they can swap out in-line valves with new ones and we’ll recondition the original valve, so they have it as a critical spare. When the next valve fails, they’ll use the reconditioned valve and continue the cycle – a proactive and budget conscious plan.


Preventative Maintenance Solutions
Preventative maintenance is crucial to minimizing downtime and managing budgets, which is why we offer preventative maintenance solutions. Working with our clients, we create a preventative maintenance plan that suits their budget and their operational requirements. Our field service trucks are equipped with pneumatic grease pumps that enable us to inject sealants and grease valves and wellheads onsite. A regular maintenance schedule like this keeps valves in good shape and flushes out impurities. Our plans include regular greasing and function testing.
Preventative Maintenance Solutions
Preventative maintenance is crucial to minimizing downtime and managing budgets, which is why we offer preventative maintenance solutions. Working with our clients, we create a preventative maintenance plan that suits their budget and their operational requirements. Our field service trucks are equipped with pneumatic grease pumps that enable us to inject sealants and grease valves and wellheads onsite. A regular maintenance schedule like this keeps valves in good shape and flushes out impurities. Our plans include regular greasing and function testing.

Plunger Lift Systems & Lubricators
We provide detailed inspections, lubricator repairs and replacements, and wellhead component (e.g. Flow Cross, Tubing, Catcher Assembly) repairs and replacements on Plunger Lift Systems. Plunger Lift Systems de-liquify and optimize natural gas wells and are designed to bring contaminants to the surface at set times in order to maximize gas production. Keeping these systems at peak performance is crucial to efficiency as these systems wear naturally with use and time.


Valve Modifications and Reconditioning
We offer valve modifications and reconditioning on all types, brands, and sizes of valves. Modifications enhance valve functionality, upgrade the valve materials, and provide a better, more cost-effective solution for extreme or corrosive service. Valve materials and internals that we typically upgrade include
- Seals: changing out standard seals/elastomer compounds with upgraded seals for longevity in severe service.
- Seat Inserts: changing out standard seat inserts for better service compatibility and seal ability (e.g. Standard Nylon Seats that conflict with concentrations of H2S & CO2 are swapped out for PEEK Seat Material).
- Body Coating: applying coating to valve bodies and components to protect from corrosive service, ensuring enhanced function, and valve performance longevity (e.g. high phosphorous nickel coating in valve seat pockets to protect from damage caused by acid gas).
- Actuator Installation: converting valves from manual operation to actuated applications for customers that require remote operation, full automation, or ESD applications in case of emergency situations or regulatory purposes.
Most of the upgraded parts that we install come from the original equipment manufacturer and/or meet or exceed the OEM’s and our customers specifications. We often strengthen valve materials for corrosive service, ensuring that the metallurgy, soft components, seals, and stem seals are stronger.
Valve Modifications and Reconditioning
We offer valve modifications and reconditioning on all types, brands, and sizes of valves. Modifications enhance valve functionality, upgrade the valve materials, and provide a better, more cost-effective solution for extreme or corrosive service. Valve materials and internals that we typically upgrade include
- Seals: changing out standard seals/elastomer compounds with upgraded seals for longevity in severe service.
- Seat Inserts: changing out standard seat inserts for better service compatibility and seal ability (e.g. Standard Nylon Seats that conflict with concentrations of H2S & CO2 are swapped out for PEEK Seat Material).
- Body Coating: applying coating to valve bodies and components to protect from corrosive service, ensuring enhanced function, and valve performance longevity (e.g. high phosphorous nickel coating in valve seat pockets to protect from damage caused by acid gas).
- Actuator Installation: converting valves from manual operation to actuated applications for customers that require remote operation, full automation, or ESD applications in case of emergency situations or regulatory purposes.
Most of the upgraded parts that we install come from the original equipment manufacturer and/or meet or exceed the OEM’s and our customers specifications. We often strengthen valve materials for corrosive service, ensuring that the metallurgy, soft components, seals, and stem seals are stronger.

Hydrostatic Valve Testing
Hydrostatic testing ensures that valve integrity and functionality is maintained throughout the valve reconditioning, rebuilding, and modification process. We provide inspection and test reports to all our customers and we routinely perform hydrostatic tests for other valve companies and distributors for customers that require additional testing. Not only is hydrostatic testing regulatory, but it also gives peace of mind that what we build works – it allows us to test the integrity of our work and the products we sell.
We provide hydrostatic testing on all valve types, brands, and sizes from ½” to 60”. We currently have four Hydrostatic Test Units, three High Pressure Hydrostatic Test Presses, and one Mobile Hydrostatic Test Unit. We follow API 6D, API 598, and CSA Z245.15-01 testing standards, and perform the following tests when necessary for specific valve applications: shell tests, seat tests (high pressure and low pressure), double block and bleed tests, double isolation tests and backseat tests.


Valve and Actuator Sales
Dynamic Valve Service is proudly a “one-stop-shop” for valve and actuator repair and replacement. Not only do we repair, modify, recondition, and test valves and actuators, but we also keep a large inventory in our shop. Plus, we have strong relationships with local distributors that allow us to source products we don’t have in stock.
Valve and actuator issues can cause costly downtime.
We solve these problems for you.
Valve and Actuator Sales
Dynamic Valve Service is proudly a “one-stop-shop” for valve and actuator repair and replacement. Not only do we repair, modify, recondition, and test valves and actuators, but we also keep a large inventory in our shop. Plus, we have strong relationships with local distributors that allow us to source products we don’t have in stock.
Valve and actuator issues can cause costly downtime.
We solve these problems for you.

Contact Us
Corporate and Accounting Office
3910-77 Ave, Leduc T9E 0B6
Main Facility
3910 - 77th Avenue, Leduc T9E 0B6
(780) 803-5580
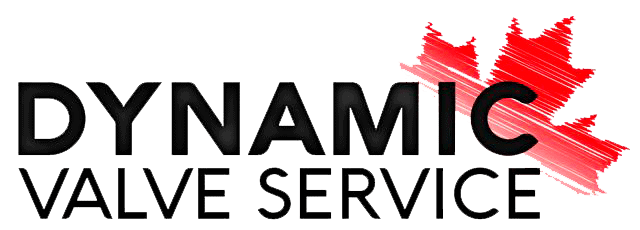